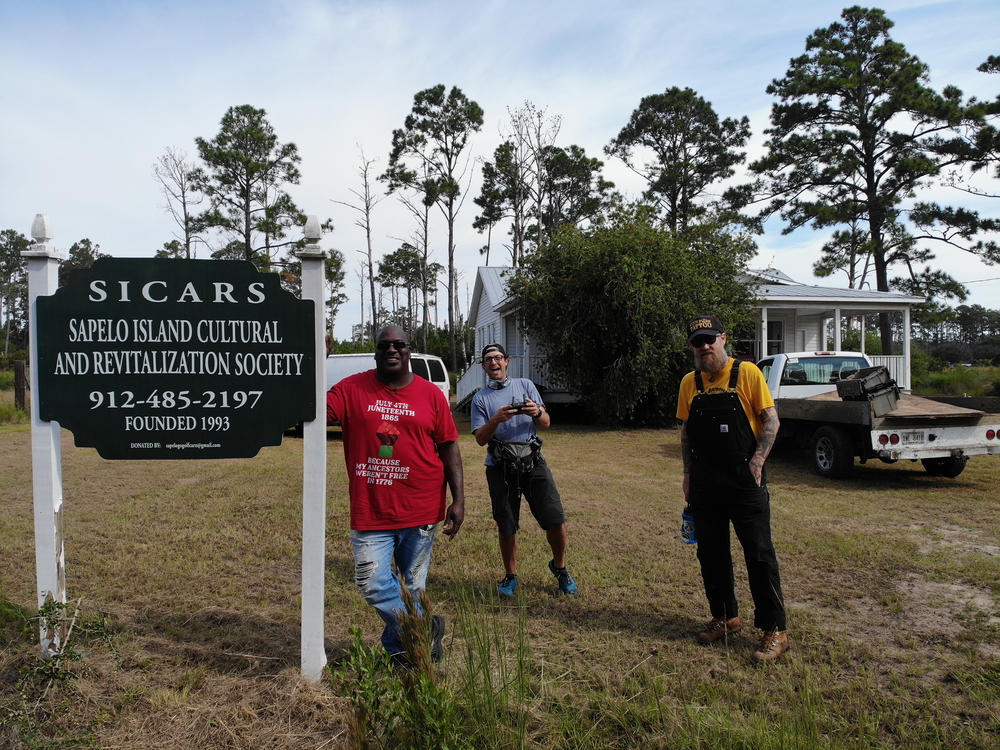
Section Branding
Header Content
A Fork in the Road Podcast: Sapelo Island Cultural Revitalization Society - Part 2
Primary Content
Sapelo Island is home to the last intact Gullah Geechee community in the Sea Islands of Georgia. It is comprised of direct descendants of slaves that were brought here in 1802. In this episode, we're going to learn how exactly a green plant turns into the bluish-purple color used to dye denim and how that plant is helping to revive a small island community off the Georgia coast.
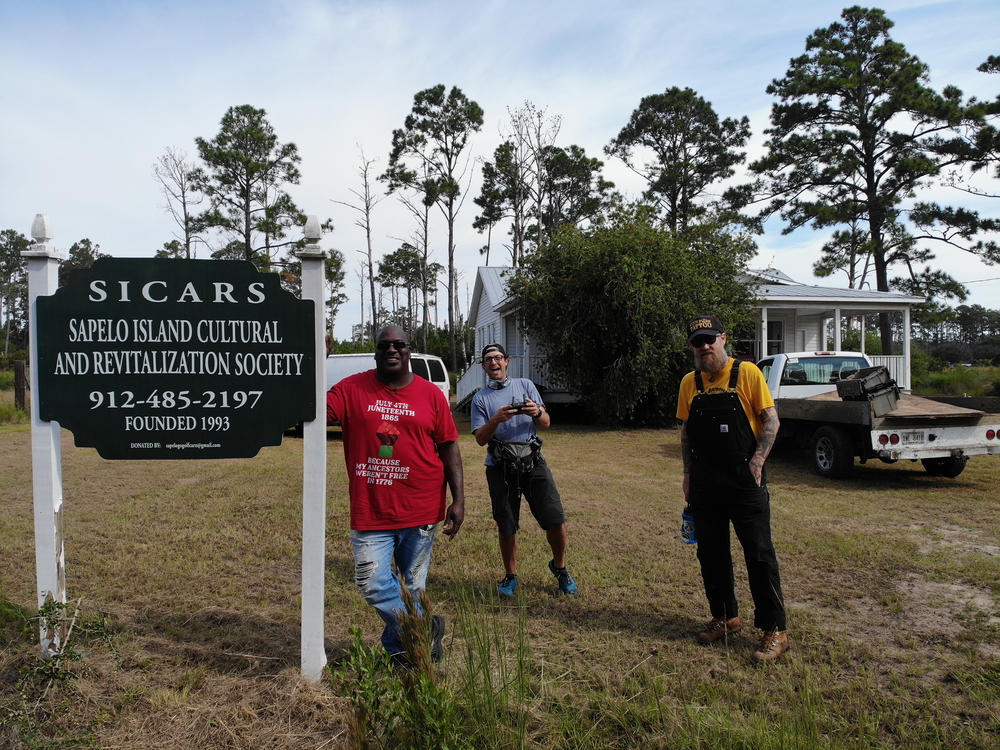
(TRANSCRIPT)
Dr. Nik Heynen: We are doing our first experimental processing of Sapelo grown indigo.
Maurice Bailey: From a green plant to a blue dye. All natural.
David Zelski: When I say indigo, what color do you think of? Not sure? Well, what if I were to say "blue jeans?" Now, what color do you picture? Can you see that bluish color in your mind? Well, in this episode, we're going to learn how exactly a green plant turns into the bluish-purple color used to dye denim and how that plant is helping to revive a small island community off the Georgia coast.
Theme Song: I came from the mud, there's dirt on my hands. Strong like a tree, there's roots where I stand.
David Zelski: I'm David Zelski, and this is the Fork in the Road podcast, featuring the stories of Georgia's farmers, fishermen, merchants, artisans, chefs and others who help provide Georgia-grown products to folks in the Peach State and beyond. This is the second episode in a special two-parter with Maurice Bailey and Dr. Nik Heynen on Sapelo Island, a barrier island 60 miles south of Savannah, Ga.'s coast. The 12-mile island is home to the last intact Gullah Geechee community in the Sea Islands of Georgia, and is comprised of direct descendants of slaves that were brought here in 1802.
Maurice Bailey: I hope this all works. Some people wasn't keen on the idea of bringing indigo back and doing indigo because of the history of it. Well, we're hoping to show that now we can actually make money off of it instead of looking at a negative thing now, to be a positive spin.
David Zelski: Now, here's a short recap. In the first episode, we learned that the Sapelo Island Cultural Revitalization Society is bringing back red peas, sugar cane, and a miracle herb called life everlasting. But that's not all. They're also reintroducing indigo as a potential cash crop.
Maurice Bailey: So hopefully this successful trial we do right here, we could gain the support of more people with this project on the island.
David Zelski: We are with Maurice and Dr. Nik as they attempt to make indigo dye for the very first time. While indigo is used for tea, taken to help support your immune system, it is most commonly known as a dye for both hair and fabrics. Dr. Nik and Maurice have a plan.
Dr. Nik Heynen: Well, I think our plan is to develop a market capacity through niche textile artists. A lot of folks are interested in kind of bringing back more craft dyeing. And I think with the Sapelo history and SICARS backing it, I just feel like a lot of folks will be very interested. We've already started to see a lot of interest in it, so.
David Zelski: Growing red peas, sugar cane, and life everlasting is pretty straightforward. But growing and processing indigo seems different. How did this come about?
Dr. Nik Heynen: A woman named Donna Hardy, who is the president of the International Center for Indigo Culture, started talking with Maurice and I, along with a woman named Gareth Crosby, who is in charge of the Heritage Garden at the Botanical Garden for the state of Georgia. And we started having a conversation that really went back to his mother, who wanted to have indigo be one of the crops that SICARS brought back. They came up strong last last year when we planted the first batch, but we didn't know how to process it properly and we weren't prepared. And so this off season, we've worked with Donna to get all the other materials necessary. And so as — as you'll see here in a little bit, we started we did do the cut in from the top and our process. And, we'll head over to his house right now.
David Zelski: Large buckets or vats, whisks, lime, muslin, water. They're simple materials, but they all have specific functions in the process. Now, let's follow along as Dr. Nik and Maurice try this out for the very first time.
Dr. Nik Heynen: We are doing our first experimental processing of Sapelo-grown indigo, and we just cut all this Wednesday morning from that stand.
Maurice Bailey: We had this soaking for two days. Just got to wait for the fermentation time. Depends on the temperature. Look for the — the layer on top and look for the bubbles. Then we know it's time to screen it and go to the next step.
Dr. Nik Heynen: And so we're pouring out the vegetation to get to the core liquid. It's been sitting for two days, heating up, starting the fermentation process. It is pungent.
Maurice Bailey: Yeah it is.
Dr. Nik Heynen: The very first time we've ever done this is happening right now. We have been talking about this for five years. So after growing the first patch last year and figuring out the process, kind of got everything together, this is it.
David Zelski: Let's stop a minute and recognize the work they have put into this project. Five years. Five years is how long it took to make this experiment happen. That is 1,825 days. That is longer than you were in high school. Yeah, I like that. Yeah. So with one patch of indigo to process, how much dye can be made out of it? Because it sure doesn't look like much.
Maurice Bailey: It doesn't look very concentrated. Yeah, this is our first time. It doesn't look very concentrated. So, I imagine once it's dry, we might — we don't know how much dye we're going to get, but out of this it won't be much.
Dr. Nik Heynen: Evaporated a lot out. So, we'll get back to just essentially the grain. The granular pigment in a dust form is — is ultimately the dye.
David Zelski: So if you got to selling.
Dr. Nik Heynen: It would be a very small unit size that we would probably sell. I mean, they sell it all kinds of different industrial sizes, but they're, you know, mass producing with machines and factories, so.
David Zelski: So if this does well, how far down the road do you see this becoming viable for y'all?
Maurice Bailey: Next year. If this works, we've got enough seeds, enough land that we could produce enough indigo next year.
Dr. Nik Heynen: Start to take to market?
Maurice Bailey: Yeah.
David Zelski: It seems to me that they are on the path to a new market product. Georgia-Grown Indigo.
Dr. Nik Heynen: This is a race. So the point of this is that we aerate the liquid until it turns brown.
David Zelski: And what is aeration? Well, a quick search on the Google machine says it is the process by which air is circulated through, mixed with, or dissolved in a liquid or substance. During this portion of the indigo dye-making process, you whisk the vat for 10 to 15 minutes until the froth turns blue and then brown, meaning it has enough oxygen. Okay, back to Maurice and Dr. Nik.
Dr. Nik Heynen: Then we add the lime pickling line to get the pH up to 11 is what it has to be to go into this next phase.
Maurice Bailey: All right. Pour number one of seven.
Dr. Nik Heynen: 15.
Maurice Bailey: Okay.
Dr. Nik Heynen: That's two.
Maurice Bailey: Yeah. So we should keep note of.
Dr. Nik Heynen: Yeah, we should do a pH reading first.
Maurice Bailey: Yeah.
Dr. Nik Heynen: And then real slowly add. So I guess we probably need a spoon.
Maurice Bailey: And how much we have.
Dr. Nik Heynen: Yeah, yeah, yeah, exactly.
Maurice Bailey: I got like 12 quarts. Yeah.
Dr. Nik Heynen: Yeah.
David Zelski: Tell me what you're doing now.
Maurice Bailey: Testing the pH and see how much lime we need to add to it. And I don't see any really major coloration.
Dr. Nik Heynen: Looks like six. Wait, I'm going to change it.
David Zelski: What does the lime do?
Dr. Nik Heynen: The — the acidic increase in acidity is central to the chemical process of making the dye come out of the pigment and kinda locks down that color.
David Zelski: There's a lot happening that you can't see. So allow me to break this down. First, they cut the indigo and let it soak for two days to ferment. Second, Dr. Nik and Maurice strain out the vegetation by pouring out the buckets through a strainer. Next, they aerate the liquid until it turns brown, meaning it has enough oxygen. Finally, they add lime to get the pH to 11 — which is important because it affects the color of the indigo. This is the step we're on now.
Maurice Bailey: So yeah. So did the instructions come with how long you stir?
Dr. Nik Heynen: No.
David Zelski: Gradually.
Dr. Nik Heynen: Gradually. Someone was paying attention. That's probably good, right?
Maurice Bailey: So it's going to be based on what color we actually trying to achieve so we can go darker.
Dr. Nik Heynen: We can't go darker, because if it goes darker than it has a pH above 11, we got to keep it on this side.
Maurice Bailey: Yeah, but the pH just means a darker dye. But looking for that perfect dye.
Dr. Nik Heynen: Yeah, we want the perfect dye.
Maurice Bailey: Yeah. Ok.
Dr. Nik Heynen: But seems like we could add a whole bunch more.
Maurice Bailey: But I say let's try it again. Let's do it again. Let's put some in there. Let this rest. And we test again.
Dr. Nik Heynen: We do a quarter cup in this one.
Maurice Bailey: Okay. Let's see what we —
Dr. Nik Heynen: That's the lime, right?
Maurice Bailey: Yeah.
David Zelski: So they have added the lime, and I bet you're wondering how they know what color is the right color. Well, it depends on the person. One may say it is a color between blue and violet. Merriam-Webster says indigo is a deep, reddish blue. Let's now see what it is for Maurice and Dr. Nik.
Maurice Bailey: And that is a haint blue. Yeah. For to ward off evil spirits.
David Zelski: "Haint blue." Ever heard of it? Me neither. But Wikipedia says that haint blue is a collection of pale shades of blue green that are traditionally used to paint porch ceilings in the southern United States. Now, originally, haint blue was thought by the Gullah to ward haints or ghosts away from the home. The tactic was intended to either mimic the appearance of the sky, tricking the ghost into passing through, or to mimic the appearance of water, which ghosts traditionally could not cross. The Gullah would paint not only the porch, but also doors, window frames and shutters. Okay, back to the process.
Maurice Bailey: I mean, we got this much liquid out of the little bit of plant that we harvest. And we could do it twice a year per plant.
Dr. Nik Heynen: Yeah.
Maurice Bailey: Yeah, yeah. But then we'll see how much we actually get out of all this. How much dye. They we can base on how much we can yield by how much we got from...
Dr. Nik Heynen: Yeah.
Maurice Bailey: ...these 24 quarts of liquid.
David Zelski: What's the next step?
Dr. Nik Heynen: Next step is that we screen the liquid through muslin to strain out all the particles that we can.
David Zelski: When they screen liquid through the muslin cotton fabric, it helps to remove the extra leaves and particles that are left behind.
Maurice Bailey: We are transferring it. So as we do the final screening, we have it in this clear one. So we have more visual of it. We can see it. We could see the clarity of it, see the color of it compared to being in this white bucket..
Dr. Nik Heynen: The settling of the the, the — the pigment.
Maurice Bailey: The pigments. Yeah.
David Zelski: Now that we are at the end of the first indigo experiment for Maurice and Dr. Nik, let's see if they think it was a success.
Maurice Bailey: Now I'm very pleased to see the color, so I think it's a success for us being amateurs.
David Zelski: Not for long.
Dr. Nik Heynen: Mad scientists.
Maurice Bailey: Not for long. Next year we will have this down pat.
Dr. Nik Heynen: The light coming up on on it. It's just this is like straight up indigo.
Maurice Bailey: Yeah.
Dr. Nik Heynen: The definition of indigo, which it should be. So I share Maurice's feeling of success. Georgia-grown indigo.
Maurice Bailey: From a green plant to a blue dye. All natural.
David Zelski: Yep. From a green plant to a blue dye. That's Georgia-grown indigo from Sapelo Island. And if you enjoyed this episode of the podcast, there's plenty more content just like it. You can watch A Fork in the Road on GPB TV or any time on the GPB.org website. GPB.org/Podcasts is where you can listen to and subscribe to this podcast or download it on your favorite podcast platform. I'm David Zelski. Thanks for listening to A Fork in the Road.
The A Fork in the Road TV show airs Saturdays at noon and Sundays at 6:30 a.m. on GPB-TV. Check your local listings for other replays throughout the week and watch all episodes anytime at GPB.org/ForkintheRoad. Please download and subscribe to the Fork in the Road podcast at GPB.org/ForkintheRoadpodcast or on your favorite podcast platform as well.
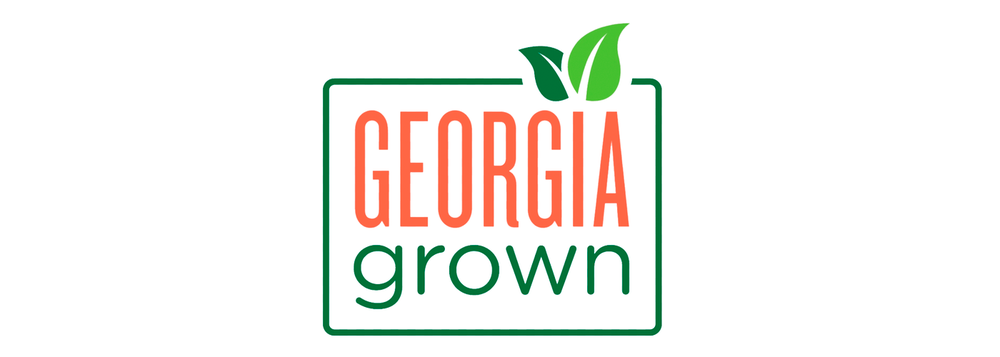
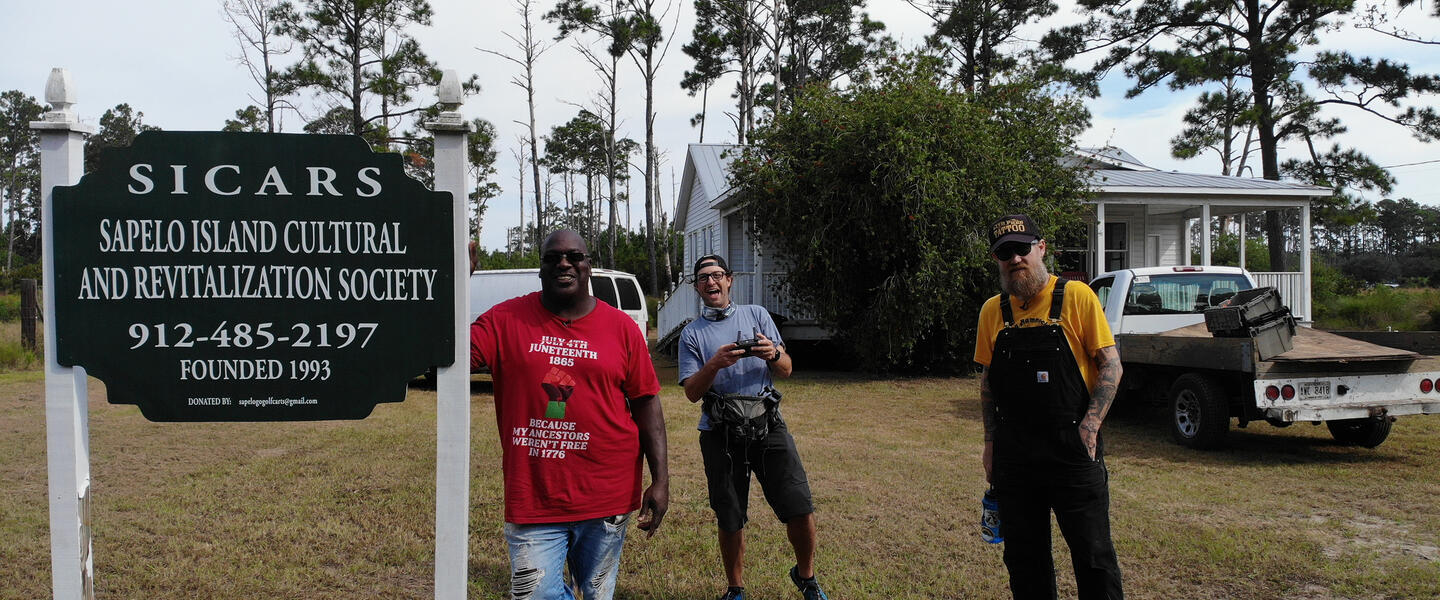