
Section Branding
Header Content
Re-defining Art And Fashion Through 3D Printing
Primary Content

A new technology could make buying your clothes at the mall a thing of the past. It's the first 3D printer that can produce fabric.
In less than a decade, the price of using printing technology has decreased by as much as $10,000, making it more accessible to the public and industries that may not have used it at its inception.
As a result , 3D printing is beginning to make significant impact on the world of art and fashion.
The buzz of the 3D printers called Makerbots can be heard several feet down the hall from the Tech Lab at Savannah's Armstrong State University.
The creative space gives students more access to the emerging technology. Now, just months after opening, the school has received a grant that will fund a series of workshops about technology in fashion. Rachel Green is a professor of Fiber Arts.
“3d printing has been applied to a wide variety of fields and recently its been applied to making wearables.”
“Wearables” or printed accessories are becoming more common, and it’s giving designers more flexibility to create.
(See a Video of the 3D Printers in Action Below)
Professor Angela Horne said 3D printing is a way to take design to the next level. She points to a picture of a dress with brightly colored material melded into the fabric. It’s the work of a 3Doodler.
“It looks like a fat marker or a handheld dremel tool,” she explains. “So you can literally sculpt in midair.”
And clothing design isn’t the only place in the art world seeing 3D.
Kristen Baird is the owner of Jewelry by Kristin Baird in Savannah.
Her jewelry design program called autoCAD or CAD for short allows Baird to view a finished version of her piece on the computer before she’s actually made the jewelry.
“I can show somebody a $10,000 ring before I buy the stones before I purchase the metal before I spend any fees on labor for getting it cast and set…I can show them, this is what it will look like…and that’s an easier way than you having this very expensive piece you’ve already bought all your stones you’ve got $10,000 worth of diamonds already tied up and then they change their mind.”
The software allows the user to create multiple pieces of jewelry with computer level precision. Baird even designed her own engagement ring.
I wanted to find out how much money the system saved designer so I asked several Savannah jewelers. Many I spoke with say they preferred to stick to traditional methods of jewelry creation, but Designer Omar Portigliatti is different. He’s with The International Diamond Center. They’re restructuring their entire design department to incorporate 3D. He said it would save them 20-30 percent per item.
“Just on time alone and labor,” said Portigliatti. “Time is money…The turn around on a 3D creation is about 2 and a half weeks from concept to deliverable piece.”
He says the old method takes about 6 weeks.
Over at the Savannah College of Art and Design instructor Jay Song said CAD technology is a great additional tool but nothing is like the real thing.
“I don’t think nothing will replace a human being and their hands because it has it’s own characteristics.”
Song has been using 3D technology for years and said work that would have taken craftsmen 10-20 years of training to perfect, her students can make in a quarter.
But, she believes the time saved could take away from the final product.
She grabs a piece of jewelry off a display counter in the SCAD hallway.
“If I hand carve this one: of course it’s one of a kind and has the maker’s mark around it, compared to if you print it and mass produce thousands of those. It kind of loses a personal touch.”
Ruan Basson, is a Jr. at SCAD
“I see it being a replacement of certain hand fabrication techniques. I’m sure some people will be out of a job because of that but the people that learn will be the people with the jobs.”
Regardless of which method you prefer, some would argue that 3D printing allows you to be more creative. In Omar Portigliatti’s words.
"If you can design it, you can create it."
Click here to see 3D printed models of actual human beings, in a video by GPB's Grant Blankenship
Tags: gabrielle ware, 3d printing, electroloom, GPB, GPB Savannah
Bottom Content
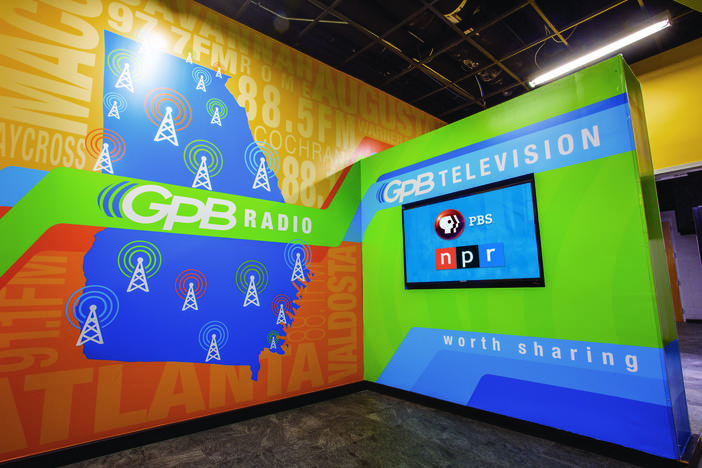